Bumper
1. Product Introduction
Kaihua Mould is a leading manufacturer of high-quality bumpers that are made using advanced manufacturing processes. Our team of experienced engineers and technicians harness the latest technologies and techniques to produce bumpers that are strong, durable, and lightweight. Our commitment to quality means you can trust our bumpers to provide superior performance and protection for your vehicle.
One of the unique aspects of our production process is our use of thin-wall molding. This technique allows us to create bumpers with thinner walls, which reduces weight while maintaining strength and durability. Additionally, we are able to produce bumpers with a wall thickness as low as 1.6mm, which further enhances performance and reduces material costs.
Another key aspect of our production process is our use of one mold with two cavities. This allows us to produce two bumpers simultaneously, which saves time and reduces costs. Furthermore, our projection area towards mold open direction is 6712mm2, which maximizes efficiency and minimizes material waste.
In terms of performance, our bumpers are designed to withstand extreme conditions and provide maximum protection for your vehicle. During the fill time, our bumpers can withstand a maximum cavity pressure of around 46.93 Mpa, which is among the highest in the industry. Additionally, our bumpers require a clamp force of 2359.10 tonne during fill time and 2359.10 tonne during cycle time.
At Kaihua Mould, we are committed to providing our customers with the highest-quality bumpers that meet their specific needs and requirements. We work closely with our clients to ensure that every bumper we produce meets their exact specifications and exceeds their expectations. Additionally, we maintain a 20% safety index to ensure that every bumper we produce is safe and reliable.
In conclusion, if you are looking for high-quality and dependable bumpers that are designed to provide superior performance and protection, look no further than Kaihua Mould. Our expertise, experience, and commitment to quality make us the ideal choice for all your bumper needs. Contact us today to learn more.
2. Advantages
· High Quality
· Short Cycle
· Competitive Cost
3. Project Cases:
4.Kaihua Mould Advantage :
Strong Industrial Design
Kaihua Car Lamp Moulds from preliminary research, to engineering design, and then to interactive design, through structural case analysis, lightweight technology reserves, ergonomics research and development, and the practice of replacing steel with plastic, the structural design and appearance design are perfectly unified.
Kaihua has obtained more than 200 patents.
Through the mastery and flexible use of Mucell, Thin Wall, Gas-Assistance, Steel To Plastic and other lightweight technology, Stack Mould, Low-Pressure Injection Molding, In-Mold Degate , Free Spraying and other high efficiency innovation technology,
Provide customers with the best solutions.
Type |
Item |
Advantage |
Customer |
Leightweight |
Mucell |
Reduce cycle time,Enhance product accuracy,
Remove sink marks, Reduce clamping force and reduce product weight |
Mercedes-Benz, Volkswagen, |
Gas Assistance |
Reduce production cost, Improve appearance |
Land Rover, |
|
Thin Wall |
Reduce production cost i.e.raw material cost/Injection production cost by reducing product weight, Enhance product dimensional stability |
Geely, Nissan, Toyota |
|
Steel to Plastic |
Reduce product weight, Reduce production cost |
Land Rover, |
|
Efficiency |
Stack Mould |
Reduce mould cost and production cost |
Audi, IKEA |
Low Pressure |
Improve the qualified rate as well as cladding sense |
Audi, Volkswagen, |
|
In-Mold Degate |
Reduce labor cost,enhance production efficiency |
Ford, Land Rover, |
|
Free Spraying |
Reduce production cost, Environmentally friendly |
Renault, GM |
Machinery
Injection Production Equipment
■ Krauss Maffei 1600T Three-color Injection Molding Machine
1) Three-color injection molding, Core Back function, DIY main nozzle translation and other functions
2) It can be applied to two-color/three-color injection of headlights, chemical foamed door panels, injection-molded compression spoilers, etc.
■ YIZUMI 3300T Injection Molding Machine with 5 Axis Pickup
■ 17 Injection Molding Machines Covering 160T ~ 4500T
Five-Axis Linkage Mold Processing Equipment
■ FIDIA, Italy
■ MAKINO, Japan
■ DMU, German
■ 12 in Total
■ ……
High Precision Spark Machine
■ DAEHAN
■ MAKINO
■ 7 in Total
MAKINO Automation lines
Name |
Function |
Application |
Time Put Into Production |
Quantity |
FIDIA GTS22 | Five-Axis Linkage CNC | Bumper & Dashboard Overall Processing | Oct. 2019 | 3 Units |
FIDIA D321 | Five-Axis 3+2 CNC | Bumper & Dashboard Overall Processing | Jan. 2020 | 4 Units |
MAKINO V90S | Five-Axis Linkage CNC | One-time Molding Of Large Top Block | Nov. 2019 | 2 Units |
MAKINO F8 | Three Axis High Precision CNC | Medium Die And Part Finishing | Oct. 2019 | 2 Units |
MAKINO A61nx | Horizontal Four-Axis High-Precision CNC | One-time Molding Of Large Top Block | Nov. 2019 | 1 Unit |
DMU 90 | Five-Axis Linkage CNC | One-step Molding Of Medium-sized Top Block | Jan. 2020 | 1 Unit |
DMU 75 | Five-Axis Linkage CNC | Small Top Block Is Formed At One Time | Oct. 2019 | 2 Units |
DAEHAN Spark Machine |
Four-Head Precision Spark Machine | Dashboard & Bumper Edm Processing | Sep. 2019 | 2 Units |
DAEHAN Spark Machine |
Double Head Precision Spark Machine | Dashboard & Bumper Edm Processing | Jul. 2019 | 3 Units |
MAKINO Spark Machine |
Precision Spark Machine | Mirror Edm Processing Of Mesh & Electroplated Parts | Oct. 2019 | 2 Units |
MAKINO Flexible Graphite Automatic Production Line | Precision Graphite Processing Machine | Graphite Electrode Processing | Oct. 2019 | 6 Units |
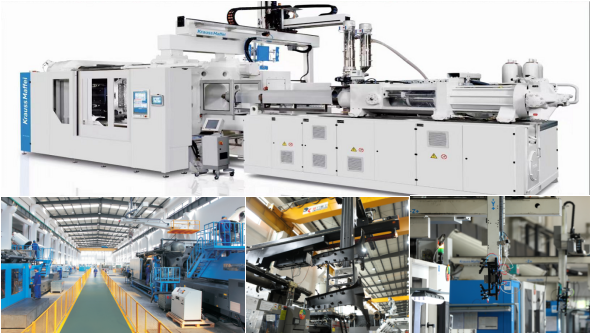
Integrated injection molding
From product research and development, mold manufacturing, to injection molding, mass production and assembly, the integration of mold injection molding is realized; the volume of injection molded parts can reach 4m², The molding cycle is short, and the surface quality is high, ensuring "fine molds" to produce "high-quality products".
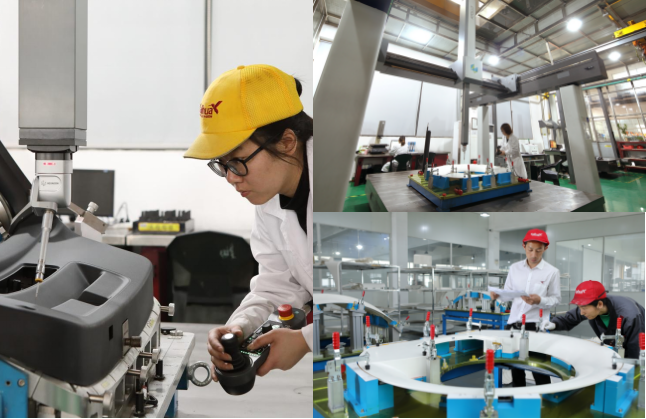
Strict Quality Control
Implement the project engineer responsibility system, set up a quality control department, and set up an incoming material inspection team, a CMM inspection team, and a shipping and dismantling inspection team. Effectively control quality and progress.
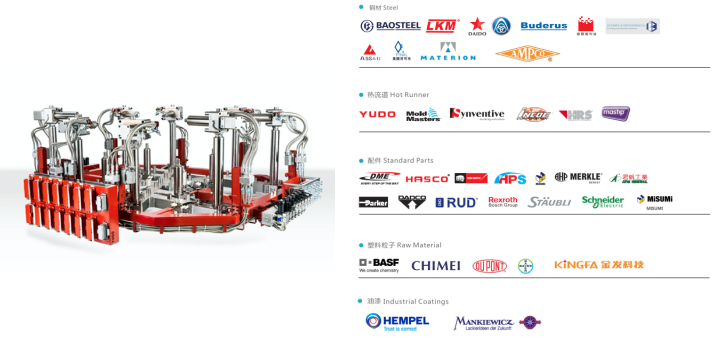
Top Partner
Frequency Asked Questions
Q: Can you do the finished product or parts Only?
A: Sure, We could do finished product according the customized mold. And make the mold also.
Q: Can I test my idea/product before committing to mould tool manufacture?
A: Sure, we can use CAD drawings to make models and prototyping for design and functional evaluations.
Q: Can you do Assemble?
A: Of cause we could do. Our factory with assembly room.
Q: What shall we do if we do not have drawings?
A: Please send your sample to our factory,then we can copy or provide you better solutions. Please send us pictures or drafts with dimensions(Length,Hight,Width),CAD or 3D file will be made for you if placed order.
Q: What type of mould tool do I need?
A: Mould tools can be either single cavity (one part at a time) or multi-cavity (2,4, 8 or 16 parts at a time). Single cavity tools are generally used for small quantities, up to 10,000 parts per year whereas multi-cavity tools are for larger quantities. We can look at your projected annual requirements and recommend which would be best for you.
Q: I have an idea for a new product, but not sure if it can be manufactured. Can you help?
A: Yes! We are always happy to work with potential customers to evaluate the technical feasibility of your idea or design and we can advise on materials, tooling and likely set-up costs.
Welcome your inquires and emails.
All inquires and emails will be replied within 24 hours.