Car Door Panel Injection Mould with Gas Assistance Technology
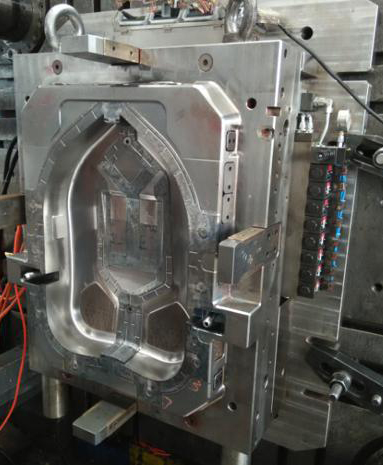

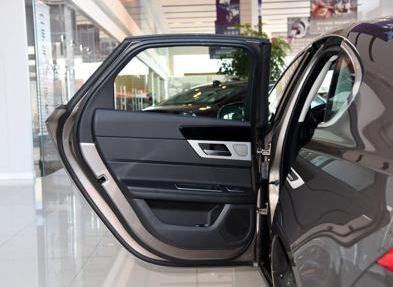
Looking for a professional and efficient solution for your automotive molding needs? Look no further than Kaihua Mould! With years of experience as a leading manufacturer of Car Door Panel Injection Mould, we pride ourselves on delivering top-quality products at a lower cost than our competitors.
One of our standout technologies is Gas Assistance, which can be applied to a wide range of plastic products, including automotive handles, door panels, and tailgate upper trim panels. With Gas Assistance, we are able to create more precise and intricate designs, while also improving the overall quality and strength of the finished product.
So if you're looking for the best in automotive mold manufacturing, trust Kaihua Mould and our Gas Assistance technology to deliver unparalleled results.
1. Product Introduction
Car Door Panel Injection Mould with Gas Assistance Technology - Enhancing Automotive Mould
As the automobile industry continues to grow, the demand for high-quality automotive moulds is also increasing. There is an urgent need for automotive manufacturers to ensure that their products meet the highest standards of quality and efficiency while maintaining a competitive edge. In this regard, the development of Car Door Panel Injection Mould with Gas Assistance Technology has become a game-changer in the automotive industry.
Kaihua Mould, a professional mold manufacturer, is leading the way in this field by providing innovative solutions to industrial problems while providing lower cost and more efficient quality solutions. With the advancement in technology, Gas Assistance technology has become an essential tool for creating automotive plastic components that are lightweight, durable, and of high quality.
What is Gas Assistance Technology?
Gas Assistance Technology is a manufacturing process that uses compressed gas to create hollow or partially hollow plastic components. In this process, the melted plastic is injected into the mold cavity, and compressed gas is injected into the mold core using a special gas channel system. The gas then displaces the molten plastic in the core to create an empty space, which is then filled with more melted plastic.
This process offers various advantages over conventional mold injection techniques. The most significant benefits include reduced waste, rapid cycle times, and more consistent part quality. Additionally, the application of Gas Assistance Technology in the automotive industry has brought about significant improvements in the production of vehicle parts such as handles, door panels, and tailgate upper trim panels.
Car Door Panel Injection Mould with Gas Assistance Technology
Car Door Panel Injection Mould with Gas Assistance Technology has become an essential component in automotive mould manufacturing. The Car Door Panel is an important part of any vehicle, and its production requires highly specialized equipment and techniques. The use of Gas Assistance Technology in the molding process brings about significant improvements in the overall quality of the product.
The Car Door Panel Injection Mould with Gas Assistance Technology provides automakers with a wide range of advantages over conventional molding techniques. With this technology, manufacturers can produce car door panels with exceptional quality, while reducing material waste, cost, and cycle times. The end product is a high-quality, lightweight, and durable product with excellent surface finish and dimensional accuracy.
Conclusion
The use of Gas Assistance Technology in the manufacturing process of automotive plastic components has revolutionized the automotive industry, ensuring that automakers produce high-quality products that meet world-class standards. As a frontrunner in the field of mold manufacturing, Kaihua Mould has been providing innovative solutions to the automotive industry, helping manufacturers reduce their costs, increase their efficiency, and improve their overall productivity.
The Car Door Panel Injection Mould with Gas Assistance Technology is an excellent example of the innovative products offered by Kaihua Mould, which provides cost-efficient and high-quality solutions to automotive manufacturers worldwide. With the ever-growing demand for high-quality automotive parts, the use of advanced technology such as Gas Assistance Technology is poised to change the face of automobile manufacturing forever.
Advantages of Gas Assistance injection mold
1. Save raw materials, improve plastic utilization and reduce molding cycle.
2. It can reduce the pressure in the mold, make the size of the workpiece uniform, and improve the shrinkage deformation.
3. Reduce the working pressure of the injection system and mold locking system of the injection machine, make the mold suitable for smaller machines and reduce power consumption.
2. Advantages of Kaihua Moulds
· High Quality
· Short Cycle
· Competitive Cost
3. Product Parameter (Specification)
4. Project Cases:
5. Kaihua Mould Advantage :
Strong Industrial Design
Kaihua Car Lamp Moulds from preliminary research, to engineering design, and then to interactive design, through structural case analysis, lightweight technology reserves, ergonomics research and development, and the practice of replacing steel with plastic, the structural design and appearance design are perfectly unified.
Kaihua has obtained more than 200 patents.
Through the mastery and flexible use of Mucell, Thin Wall, Gas-Assistance, Steel To Plastic and other lightweight technology, Stack Mould, Low-Pressure Injection Molding, In-Mold Degate , Free Spraying and other high efficiency innovation technology,
Provide customers with the best solutions.
Type |
Item |
Advantage |
Customer |
Leightweight |
Mucell |
Reduce cycle time,Enhance product accuracy,
Remove sink marks, Reduce clamping force and reduce product weight |
Mercedes-Benz, Volkswagen, |
Gas Assistance |
Reduce production cost, Improve appearance |
Land Rover, |
|
Thin Wall |
Reduce production cost i.e.raw material cost/Injection production cost by reducing product weight, Enhance product dimensional stability |
Geely, Nissan, Toyota |
|
Steel to Plastic |
Reduce product weight, Reduce production cost |
Land Rover, |
|
Efficiency |
Stack Mould |
Reduce mould cost and production cost |
Audi, IKEA |
Low Pressure |
Improve the qualified rate as well as cladding sense |
Audi, Volkswagen, |
|
In-Mold Degate |
Reduce labor cost,enhance production efficiency |
Ford, Land Rover, |
|
Free Spraying |
Reduce production cost, Environmentally friendly |
Renault, GM |
Machinery
Injection Production Equipment
■ Krauss Maffei 1600T Three-color Injection Molding Machine
1) Three-color injection molding, Core Back function, DIY main nozzle translation and other functions
2) It can be applied to two-color/three-color injection of headlights, chemical foamed door panels, injection-molded compression spoilers, etc.
■ YIZUMI 3300T Injection Molding Machine with 5 Axis Pickup
■ 17 Injection Molding Machines Covering 160T ~ 4500T
Five-Axis Linkage Mold Processing Equipment
■ FIDIA, Italy
■ MAKINO, Japan
■ DMU, German
■ 12 in Total
■ ……
High Precision Spark Machine
■ DAEHAN
■ MAKINO
■ 7 in Total
MAKINO Automation lines
Name |
Function |
Application |
Time Put Into Production |
Quantity |
FIDIA GTS22 | Five-Axis Linkage CNC | Bumper & Dashboard Overall Processing | Oct. 2019 | 3 Units |
FIDIA D321 | Five-Axis 3+2 CNC | Bumper & Dashboard Overall Processing | Jan. 2020 | 4 Units |
MAKINO V90S | Five-Axis Linkage CNC | One-time Molding Of Large Top Block | Nov. 2019 | 2 Units |
MAKINO F8 | Three Axis High Precision CNC | Medium Die And Part Finishing | Oct. 2019 | 2 Units |
MAKINO A61nx | Horizontal Four-Axis High-Precision CNC | One-time Molding Of Large Top Block | Nov. 2019 | 1 Unit |
DMU 90 | Five-Axis Linkage CNC | One-step Molding Of Medium-sized Top Block | Jan. 2020 | 1 Unit |
DMU 75 | Five-Axis Linkage CNC | Small Top Block Is Formed At One Time | Oct. 2019 | 2 Units |
DAEHAN Spark Machine |
Four-Head Precision Spark Machine | Dashboard & Bumper Edm Processing | Sep. 2019 | 2 Units |
DAEHAN Spark Machine |
Double Head Precision Spark Machine | Dashboard & Bumper Edm Processing | Jul. 2019 | 3 Units |
MAKINO Spark Machine |
Precision Spark Machine | Mirror Edm Processing Of Mesh & Electroplated Parts | Oct. 2019 | 2 Units |
MAKINO Flexible Graphite Automatic Production Line | Precision Graphite Processing Machine | Graphite Electrode Processing | Oct. 2019 | 6 Units |
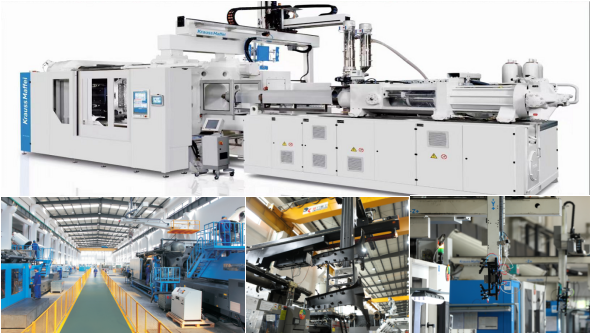
Integrated injection molding
From product research and development, mold manufacturing, to injection molding, mass production and assembly, the integration of mold injection molding is realized; the volume of injection molded parts can reach 4m², The molding cycle is short, and the surface quality is high, ensuring "fine molds" to produce "high-quality products".
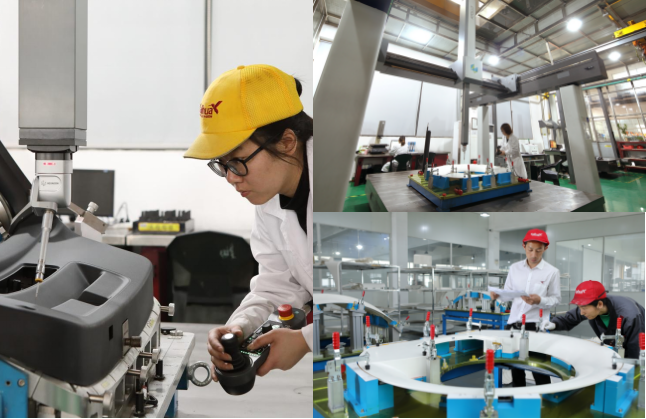
Strict Quality Control
Implement the project engineer responsibility system, set up a quality control department, and set up an incoming material inspection team, a CMM inspection team, and a shipping and dismantling inspection team. Effectively control quality and progress.
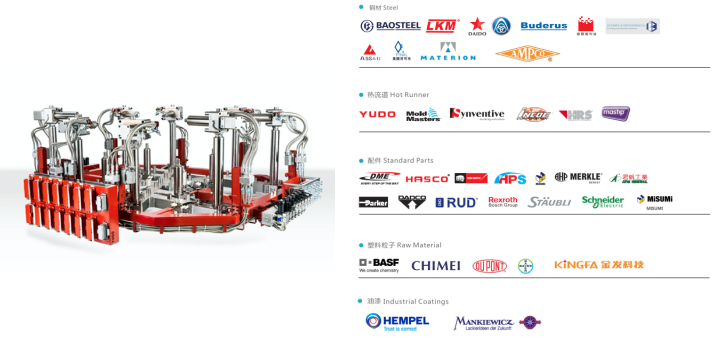
Top Partner
Frequency Asked Questions
Q: Can you do the finished product or parts Only?
A: Sure, We could do finished product according the customized mold. And make the mold also.
Q: Can I test my idea/product before committing to mould tool manufacture?
A: Sure, we can use CAD drawings to make models and prototyping for design and functional evaluations.
Q: Can you do Assemble?
A: Of cause we could do. Our factory with assembly room.
Q: What shall we do if we do not have drawings?
A: Please send your sample to our factory,then we can copy or provide you better solutions. Please send us pictures or drafts with dimensions(Length,Hight,Width),CAD or 3D file will be made for you if placed order.
Q: What type of mould tool do I need?
A: Mould tools can be either single cavity (one part at a time) or multi-cavity (2,4, 8 or 16 parts at a time). Single cavity tools are generally used for small quantities, up to 10,000 parts per year whereas multi-cavity tools are for larger quantities. We can look at your projected annual requirements and recommend which would be best for you.
Q: I have an idea for a new product, but not sure if it can be manufactured. Can you help?
A: Yes! We are always happy to work with potential customers to evaluate the technical feasibility of your idea or design and we can advise on materials, tooling and likely set-up costs.
Welcome your inquires and emails.
All inquires and emails will be replied within 24 hours.